In the June, 2019 issue of Electrical Apparatus Magazine, a reader asked the editors: Is there any standard test to show whether or not any damaging shaft/bearing currrents are present in a motor? The short answer is No. But we'd like to take a few moments to expand on why there's no practical way to measure bearing current directly, and to explore the viable alternatives.
By definition, bearing current is the flow of current from the shaft, through the bearing, to the motor frame. But a bearing is not normally conductive. When current manages to pass through, it's in the form of an arc. This arcing damages the bearing by roughening it. (Hence the problem, and our interest!)
In order to measure bearing current, you'd need to insert some type of sensor either between the shaft and the bearing, or between the bearing and the frame, such that all of the bearing current passed through the sensor. There are a few problems with this, but one stands out: This would not be practical to do in the field! It has been done, but only in the lab.
In spite of some misleading marketing, Rogowski coils do not measure bearing current. These are often used on variable frequency drive output to the motor, to measure the total high frequency "common mode" (CM) current going to the motor. While some of this CM current may pass through the bearings, bearing current is only a small portion of the total. The relationship between CM current and bearing current is complicated. You can't simply say that 1% or 10% goes through the bearings; there are too many variables. Rogowski coils also suffer sensitivity problems with high-frequency bearing current. Standard coils for power frequency current are too slow, and faster coils can overshoot, giving measurements 300-400% too high.
To some extent, bearing current can be measured with discharge detector pens. Bearing currents produce bursts of radio static, and these pens detect those bursts. But in electrically noisy environments, with many motors and drives, these pens can give erratic results. The pens are also sensitive to distance from the bearing. If you detect no discharges, you may be holding the wand too far from the bearing; if you do detect discharges, they might be real, or it might be radio noise from other sources. You can't be sure without a second type of measurement for confirmation.
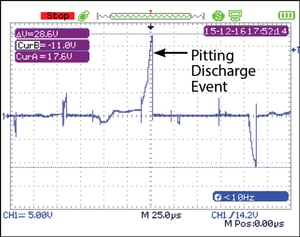
So then what can you measure?
Well, all current is driven by voltage. And you can measure the voltage across the bearing by measuring the voltage difference between the motor shaft and frame, a.k.a. the shaft voltage. You can indirectly measure bearing current by looking for sudden collapses in shaft voltage. These indicate a discharge (arc) through the bearings.
You can measure shaft voltage with an oscilloscope like the AEGIS Shaft Voltage Tester, or any scope with bandwidth of at least 100 MHz. Multimeters don't work because shaft voltage changes too quickly. With a scope, you can both see the shaft voltage level, and see when a bearing current occurs.
Gunnar Englund and more recently Fluke have developed devices that can both detect and count shaft voltage discharges. Englund's Bearing Predictor (Beppe) and Fluke's MDA-550 both use statistical models to predict whether the bearings will fail prematurely, based on bearing current levels. These are powerful tools, but they are more costly than a standard oscilloscope.
Whatever method you use to measure shaft voltage, the measurement should be made under normal operating conditions, especially rpm, load, and temperature. Motors will show different levels of shaft voltage and bearing current depending on those three factors.
In summary, bearing current cannot feasibly be measured directly. There are practical problems with measuring the current itself, and it's hard to reliably detect the radio signals it produces. Bearing current must be inferred based on shaft voltage measurements using an oscilloscope. The measurements can be made manually with a general purpose scope, or automatically with a higher-end specialized instrument.
AEGIS Rings also come with a 2-year extended warranty against bearing fluting damage. No other form of protection against VFD-caused bearing damage offers a warranty like this.
To learn more about AEGIS shaft grounding and best practices for electrical bearing protection, sign up for a training. We offer monthly live training webinars, and we can also visit your facility to review your exact application.