Q1. We have a 5000 hp dc motor, running at 40 rpm. Is there an AEGIS® ring suitable for this machine?
A1. Yes. To review, our SGR rings have two rows of fiber. SGRs are fine for motors up to a few hundred horsepower. The general rule for low voltage motors is 300 hp (225 kW) for dc motors, and 500 hp (375 kW) for ac. For larger motors, and medium voltage motors (over 600V), we make our PRO Series of grounding rings. PRO rings have six rows of conductive microfiber. That allows them to carry more current from the shaft. Higher fiber density means better conductance/lower impedance. And you really need that extra current capability with these larger motors.
For 5,000 hp, you definitely want a PRO ring, whether the motor is ac or dc, or low or medium voltage.
Q2. We use AEGIS rings in combination with insulated bearings on medium-sized motors. We follow your recommendations and put the grounding ring at the drive end, and insulated bearing at the non-drive end (NDE). But we have actually had some insulated bearings fail do to fluting damage. What is your experience with this?
A2. That is a rare problem, but it does happen. Remember that you use an AEGIS ring to drain off capacitive shaft voltage from the VFD, and the insulated bearing is there to interrupt high frequency circulating currents (also caused by the drive). 99% of the time, this setup works fine.
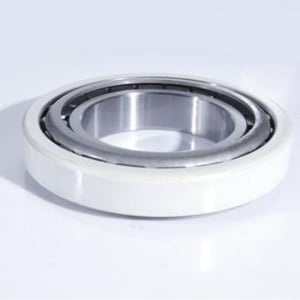
But in some cases, the insulated bearings can still be damaged by circulating current. Insulated bearings usually have a thin layer of alumina, an insulator, on the outside of the outer race. When you install this bearing in a motor, you have the motor frame, then alumina, then the steel of the bearing’s outer race: Metal, insulator, metal. That looks like a capacitor. And high frequency current can easily flow through capacitors. What happens, in these rare cases, is that circulating current flows through the alumina by capacitively charging it, and then arcs through the rolling elements and inner race. In your case, the other bearing was protected by an AEGIS ring, so the circulating current completed the loop by going through the grounding ring rather than the uninsulated bearing. That’s why only the insulated bearings failed.
So what can you do? You can solve the problem by using a ceramic bearing, aka hybrid bearing, at the NDE. These have all-metal races and ceramic rolling elements. Circulating current is not getting through a ceramic ball. But hybrid bearings are pretty expensive.
The other option is to use some type of common mode filter. Without getting too far into it, filters reduce high frequency circulating current. But they can’t eliminate it. Would they reduce it enough to prevent premature bearing failure? Maybe. They’ll certainly slow the rate of damage and prolong the NDE bearing’s life. At any rate, chokes don’t reduce shaft voltage, so you still need an AEGIS ring in this case, as well.
This has been a long answer, so to summarize: A hybrid bearing at the NDE the sure-fire way to go to protect against circulating current. 99% of the time, you’ll be fine with a cheaper insulated bearing. Common mode chokes help, but we can’t say just how much. And in any case, you need AEGIS shaft grounding to protect the drive end bearing from shaft voltage discharge.
Q3. Is high-frequency circulating current a bigger problem than low-frequency circulating current?
A3. It depends on the size of the motor and whether it’s on a drive. All electric motors can have low-frequency circulating current. But it’s only high enough to be a problem in very large motors, 500 frame or above. You can address it with an AEGIS ring at the drive end and insulated bearing at the NDE. Because it’s fairly low frequency (50/60 Hz across the line, or whatever frequency the motor’s running at on a drive), it’s less likely to require a ceramic bearing (as above). Common mode chokes will not help with low-frequency circulating current.
Medium-sized and larger motors on drives are prone to high-frequency circulating currents. By “medium” we mean over 100 hp/75 kW. These can be dealt with as above. If you have a very large motor on a drive, if you use shaft grounding at the drive end and insulation at the NDE bearing, that will take care of low- as well as high-frequency circulating currents (and shaft voltage discharge).
AEGIS Rings come with a 2-year extended warranty against bearing fluting damage. No other form of protection against VFD-caused bearing damage offers a warranty like this.
To learn more about AEGIS shaft grounding and best practices for electrical bearing protection, sign up for a training. We offer monthly live training webinars, and – pandemic restrictions permitting – we can also visit your facility to review your exact application.