Using variable frequency drives (VFDs or inverters) to control the speed of motors large and small is not only a cost-effective means of improving process/system control, it can also greatly reduce energy costs.
But VFDs have their drawbacks. They induce high frequency voltage on the shafts of the motors they control. Without an alternate path to ground, this VFD-induced voltage can discharge through motor bearings. This discharge through the bearings causes electrical discharge machining (EDM), and blasts pits into the smooth surfaces of the bearing. EDM in the bearing eventually leads to frosting and fluting (washboard-like ridges on the bearing race), and bearing failure — often in as little as 3 months!
While some large motors can be repaired on site, many must be pulled out of service, loaded onto a truck (often requiring a crane), and transported to a motor repair facility. This can be a time-consuming and very expensive process. And the larger the motor, the greater the cost of replacing damaged bearings.
But the cost of repairing motors pales in comparison to the costs of downtime and lost production. Larger motors are typically used in high volume processing applications, where the cost of every minute of lost production can be staggering.
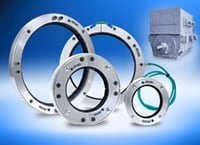
AEGIS® PRO Series Rings protect medium-voltage motors, generators, and turbines, as well as large-frame low-voltage AC motors (500 HP or greater) and DC motors (300 HP or greater). PRO Rings are vailable in solid- and split-ring versions for shaft diameters from 2.5" (50 mm) to 31.5" (800 mm). They have 6 rows of conductive microfibers that completely encircle the motor shaft, providing millions of contact points that channel harmful shaft voltages away from bearings and safely to ground.
Solid PRO Rings are best for installation on new motors before they are put into service or on older motors when they are repaired. Split PRO Rings come in mating halves that slide around the shafts of coupled motors for fast, easy field installation.
There's even an AEGIS PRO Ring for protecting and monitoring remotely located or hard-to-access motors. The AEGIS PROMR combines an PRO Ring with an monitoring ring (separated by an insulating phenolic spacer). It provides bearing protection and remote monitoring in a single, compact unit. Universal Mounting Brackets — designed to accommodate shaft shoulders, slingers, or other end bell protrusions — simplify and speed the installation of any size PRO Series Ring.
For horizontally mounted motors with single-row radial ball bearings at both ends of the motor, best practices include:
• At the non-drive end: Isolate the bearings using an insulated sleeve or coating; or install insulated ceramic or hybrid bearings to disrupt circulating currents.
• At the drive end: Install one AEGIS PRO Ring either internally (on the back of the bearing cap) or externally (on the motor end bracket).
• Whether the ring is installed internally or externally, be sure to apply AEGIS Colloidal Silver Coating to the motor shaft where the ring's conductive microfiber will make contact.
• For low- or medium-voltage motors where both bearings are insulated, install one AEGIS Ring, preferably on the drive end to protect the bearings of attached equipment (e.g., gearbox, pump, fan bearings, etc.).
For more information on AEGIS® PRO Series Rings, see the PRO Series product page. You can also peruse our case studies on how PRO Rings solved real-life problems in a number of applications.