In the article "Full speed in washdown? Not so fast!" Ron Crutchfield and Gary Jacott of Motion Industries explain the advantages of using variable frequency drives (VFDs) to provide a better way to manage energy and water in washdown systems. Published in the 03/21/2018 edition of Plant Engineering.
In this excellent article Ron and Gary discuss:
- How plants are finding ways to conserve water and energy by using VFDs
- How controlling the flow rate can also extend equipment life
- Real world examples of wash-down scenarios
- How flexibility to provide the volume and pressures can be beneficial through the use of VFDs
Ron Crutchfield has 35 years of experience as a pump engineer, and is currently senior project engineer for Motion Industries Process Pumps and Equipment in Omaha, NE. Gary Jacott has spent 30 years as an electrical engineer, including 20 years specializing in the industrial automation niche.
Selecting the Right Motor - Reliability Built-in:
One important aspect that was not specifically discussed in the article was the selection of the motor used in the washdown application. Motors operated by VFDs should have both inverter rated Class F or H winding insulation (NEMA Premium has Class F at a minimum), and shaft grounding rings installed to prevent electrical discharges in the bearings.
Whenever a motor is operated by a VFD, the voltage to the motor is a pulse width modulated series of positive and negative pulsed which cause a common mode voltage to be capacitively coupled to the motor's shaft and can result in bearing discharges. These discharges can also result in catastrophic bearing failure from "fluting" damage, shortened motor life, and expensive repairs and downtime.
|
![]()
|
![]()
|
On the bright side, all of these negative effects on the motor's bearings can be avoided by simply installing a shaft grounding ring on the motor which steers the damaging voltages away from the motor's bearings to ground. Most motor manufacturers such as ABB (Baldor), WEG, Regal, TECO, GE, and others have motors in their stock list with AEGIS shaft grounding rings installed so selecting a motor to avoid the bearing fluting issue can be quite straightforward.
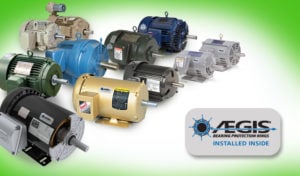
Motors can also be modified by motor repair shops to have the shaft grounding ring installed on the motor during a repair or from the start.