In the article below we are re-publishing an article written by Gunnar Englund who invented the Beppe bearing analyzer.
“All” about EDM in bearings – on one page!
What is it? EDM (Electric Discharge Machining) or Bearing Current can be caused by external current sources – like welding with return path through bearing – or internal currents and voltages caused by frequency inverters with PWM voltage output. Induced shaft voltage is predominant in larger machines while capacitively coupled voltages are at work in smaller (HVAC, mostly) machines [as well as in larger machines]. There is also the Frame Voltage, caused by high impedance in the protective earth wire. Frame Voltage is found in all motor sizes. It depends on the motor cable length and impedance.
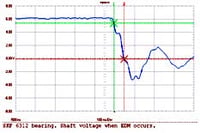
What happens? Independent on how the voltage across the bearing is produced, the discharge current always looks the same. A break-down of the oil film between balls/rollers and race-way discharges rotor capacitance and the discharge is over in .02 - .05 microseconds. Discharging the rotor capacitance in such a short time means a very high peak current – often 10 – 100 amperes. This high current heats the steel locally so that a small amount is vaporized and a small crater with diameter .5 – 1 micrometer is formed. After several millions of such craters have been formed, the surface hardness is reduced to such an extent that the balls start to bounce – like car wheels on a dirt road – and the well known wash-board pattern is formed.
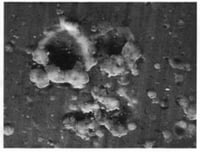
Can EDM be measured? If you look at the motor shaft voltage with an oscilloscope, you will see a mishmash of highly irregular signals. Some with low values and some voltage peaks – between 15 and 20 volts, sometimes more. It is possible to “sort out” the extremely fast edges caused by the EDM break-downs, classify them in energy levels and totalize the number of PPS in each level. That does give a number as to how critical the EDM activity in the bearing is and thence predict if the motor bearings will be destroyed by EDM or not.
It can be done with a fast digital oscilloscope. One that, in extreme real time, calculates voltage derivative and trigs and counts when a certain value is exceeded. Such oscilloscopes are rare – and costly. That is why the GKE Bearing Predictor (Beppe) has been designed and put on market. It is a small “Expert System” in a hand-held box and can be used with a minimum of training. The display “speaks” one of four selectable languages and is self-instructing. Just connect and answer a couple of questions – the Beppe does the rest.
100 nanoseconds, or faster, edges (1/10th of a microsecond) are counted and accumulated in three counters for High, Medium and Low energy. Data are stored and can be transferred to PC memory via USB.
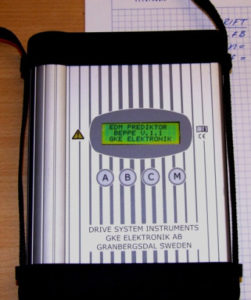
Electro Static Technology, the manufacturer of the AEGIS Shaft Grounding Ring, has had the privilege of meeting and discussing bearing currents with Gunnar Englund. The information in the article above is his own and any questions should be referred directly to him.