Part 9 in a series of questions and answers from our Q&A webinars.
Q1: Variable frequency drives can operate at different carrier frequencies. What is the best frequency to use to avoid electrical bearing damage?
A1: A little background: The carrier frequency determines how often the drive switches on and off. You typically use high carrier frequency to avoid audible noise. Basically, the carrier frequency causes the motor to vibrate (make sound). The higher the frequency, the less you can hear the resulting sound. But the higher the carrier frequency, the more often the drive switches the phase voltage on and off (Figure 1). Every time a phase switches, there's a pulse of common mode current. This common mode current causes destructive rotor ground current, and high frequency circulating current in larger motors. So high carrier frequency can increase electrical bearing damage.
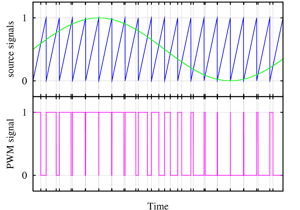
But that doesn't mean low carrier frequency prevents damage. The carrier frequency doesn't affect the common mode voltage so much. It's the common mode voltage that capacitively couples from the motor stator to the rotor to produce shaft voltage. This is the biggest problem in small, well-grounded motors. Changing the carrier frequency doesn't affect the level of the shaft voltage (only how frequently it changes). If the shaft voltage gets high enough, it will arc through the bearing, regardless of the frequency.
So the short answer is: There is no ideal carrier frequency that will prevent damage. Some people say that lower frequency reduces damage, but we've never seen a case where a user reduced the frequency and the problem went away.
What you need is good shaft grounding like an AEGIS ring and good motor grounding or motor-load bonding with a high frequency grounding strap. These will dissipate shaft voltage, and stop it from arcing through the bearing, and prevent rotor ground current. If the motor is over 100 hp/75 kW, you should also have one insulated bearing to interrupt high frequency circulating current.
Beyond that, you can set the carrier frequency to be high enough not to make too much noise.
Q2: What is the influence of motor speed on bearing current magnitude?
A2: We haven't seen that speed is a major factor. It plays in, but it's not the biggest player in the field. If a motor system is going to have a problem, it will have it whether it runs at 1500 rpm or 3000 rpm. It might be a matter of having bearing failure in five months instead of six.
Q3: What size of peak to peak shaft voltage should we be worried about?
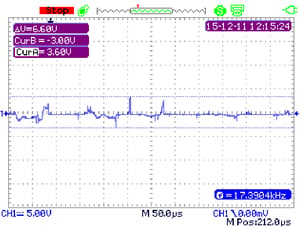
A3: There's no hard and fast answer, unfortunately. We normally say 10V peak-peak. But we've seen situations with only 2V peak-peak, but about 100,000 discharges per second. This was in an MRI cooling system. It wreaked havoc on their system after six months. But this is exceptional: normally, 2V peak-peak is totally fine.
In a motor without shaft grounding, you sometimes see low amplitude shaft voltage discharge. This seems to be because the grease is contaminated with metal and carbon particles that make it more conductive. So there's still arcing going on, but it happens at lower voltage. Damage accumulates, but because the voltage is low, it accrues fairly slowly at this stage.
We like to see shaft voltage under one volt peak. But every system is different; we've seen systems with 40-60V peak-peak and adding an AEGIS ring only brings it down to 2V. That's a win. The energy in a bearing discharge grows with shaft voltage squared, so that's a massive reduction of potentially damaging energy. If you can eliminate most of the shaft voltage, that's almost always enough.
AEGIS Rings also come with a 2-year extended warranty against bearing fluting damage. No other form of protection against VFD-caused bearing damage offers a warranty like this.
To learn more about AEGIS shaft grounding and best practices for electrical bearing protection, sign up for a training. We offer monthly live training webinars, and - pandemic restrictions permitting - we can also visit your facility to review your exact application.