Q1. What are the pros and cons of using a shaft grounding ring, as opposed to a shaft grounding brush?
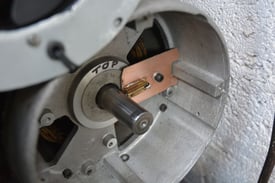
A1. Shaft grounding brushes tend to wear more than AEGIS® rings, but they are very good in some applications. They're especially good at conducting low frequency and dc current. So they've always been used in dc motor commutators. But if you've got high-frequency current - such as shaft voltage discharge, high-frequency circulating current, or rotor ground current - an AEGIS ring will work better because it has lower impedance to high frequencies. That's because high-frequency electricity travels at the surface of conductors, and there's more surface area on hundreds of thousands of microfibers than there is on a carbon brush.
In some applications, like wind turbine generators, you have high and low-frequency current flowing. For this reason, many manufacturers and wind power companies use carbon brushes and grounding rings in their turbines.
Q2. Are the fibers in a grounding ring also able to cope with dc current?
A2. Yes. It does depend on the amperage - An SGR is good for about 40 amps, and a PRO Ring can take up to 120 A. But that will change with shaft size, too. The bigger the shaft, the bigger the ring. The bigger the ring, the more conductive microfibers. And the more microfibers, the more paths are open for current to travel through, and so the more current can flow. We actually have a new case study about PRO rings discharging static on rolls in a paper mill.
Q3. Does an AEGIS ring offer more or less surface area exposed to the shaft than a carbon brush?
A3. More, sometimes a lot more. You've got a band of fibers going 360 degrees around the shaft, as opposed to a few degrees for a carbon brush. A carbon brush may be wider than that band of fibers, but you always end with more surface contact area with an AEGIS ring.
Another factor is that the shaft and brush surfaces have microscopic roughness. When installed, it looks like you've got contact all over the brush. But in reality, there's only a small percentage of the brush's surface area in actual electrical contact with the shaft. And all the current from the shaft moves through that small fraction of the brush surface. This can cause what's called hotspotting, where the contact areas end up glazed by overheating from the high current density.
With an AEGIS ring, you've got hundreds of thousands, if not millions, of microfibers in electrical contact with the shaft. They're either in physical contact with it, or they're close enough to it for non-contact grounding. (For more on non-contact grounding, see this IEEE paper.)
AEGIS Shaft Grounding Rings also have a 2-year extended warranty against bearing fluting damage. No other form of shaft grounding offers a warranty like this.
To learn more about AEGIS shaft grounding and best practices for electrical bearing protection, sign up for a training. We offer monthly live training webinars, and we can also visit your facility to review your exact application.