Electric motors are prone to many sources of damage, some more common and some better known. An increasingly common, but still not too well known, problem facing these motors is bearing current. Bearing currents damage the ball bearings with electrical discharge machining (EDM), resulting in motor failure. In addition to the repair or replacement costs of the electric motor, there is the possible loss of production caused by that motor failure. Adding it all together results in one expensive failure!
Bearing currents have been a thorn in the side of motor users for years. However, incidents are rising simply because more people are using pulse-width modulated variable frequency drives (VFDs). We will look at what bearing currents do and how to avoid them.
Bearing Currents Cause Problems
Shaft voltages damage electrical bearings when they discharge in a tiny but destructive electrical arc through the bearings. Pitting, frosting, and fluting are some of the damages caused by that current. These types of damages lead to premature bearing failure, leading to the motor failing as well. In addition, if a conductive coupling is connected to the motor drive end shaft, shaft voltage can discharge through the coupled equipment, damaging its bearing with electrical arcing.
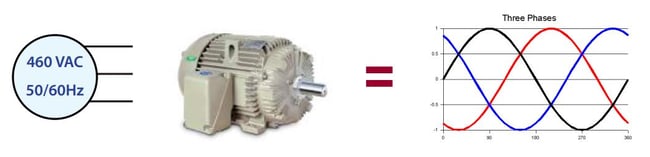
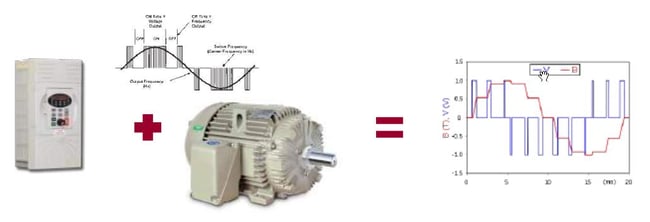
Three-phase power is what operates most AC motors. On line power, the three phases always sum to zero volts. The sum of the three phases is also called common mode voltage. The common mode voltage is zero on line power because each phase is a smooth sine wave voltage 120 degrees out of phase with the other two phases. But when a VFD is in control, each phase consists of a series of positive, zero, and negative voltage pulses. The three phases don't usually sum to zero, so the common mode voltage continuously changes with the pulses driving the motor. This nonzero common mode voltage creates shaft voltage by parasitic capacitive coupling between the stator and rotor.
And when voltage is induced onto the motor's shaft, that voltage "looks for" a least-resistance path to the ground. Usually, the path of least resistance leads through the motor's bearings. As described above, shaft voltage discharging through the bearing causes damage to EDM and cumulative electrical bearing.
Why Test Motors for Shaft Voltage?
If your facility relies on electric motors, include testing for shaft voltage in your preventative maintenance (PM) program. These tests are performed on-site, and you receive an analysis of any potential problems.
The idea behind an effective PM program is obvious: to stop issues before they become problems. Using an effective testing method for shaft voltage leads to lower cost options than repairing or replacing an expensive motor. Reducing the risk of shaft voltage reduces the risk of bearing failure and presents an opportunity to save substantial expenses.
Testing for shaft voltage is a relatively simple process. A conductive microfiber probe tip safely touches the motor's spinning shaft and captures shaft voltage data for analysis at an exposed area of the motor's shaft. Using that information, recommendations are made for courses of action. Using the AEGIS Shaft Voltage Tester is the simplest and easiest way to take shaft voltage readings. The AEGIS Best Practices Handbook explains the step-by-step procedure and many other important topics to protect your motor bearings!
AEGIS Rings also come with a 2-year extended warranty against bearing fluting damage. No other form of protection against VFD-caused bearing damage offers a warranty like this.
To learn more about AEGIS shaft grounding and best practices for electrical bearing protection, sign up for a training. We offer monthly live training webinars, and we can also visit your facility to review your exact application.