In our last post, we looked at how shaft voltage testing can be used to detect stray current arcing through motor bearings. In this post, we look at other methods of detecting bearing currents (or not).
Electrical Discharge Detection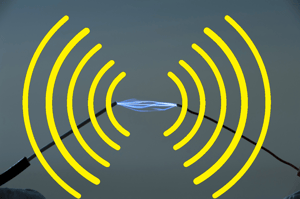
When current arcs through a dielectric – whether grease in a bearing, or air, or any other insulator – it produces a pulse of radio waves. This is how the first radio transmitters, spark gap transmitters, worked. So in theory, you should be able to detect arcing through bearings by detecting RF pulses.
And indeed you can. There is at least one electrical discharge detector on the market that uses this method. Testing is easy and nonintrusive. The device counts and reports the number of pulses detected, with the assumption that the more frequently discharge occurs, the sooner the bearing may fail. This assumption is not wrong, but it is limited – it ignores the fact that not all discharges are equally destructive. Counting pulses doesn’t tell you anything about the amount of energy each discharge releases in the bearing (which shaft voltage testing does).
But there is a bigger problem with these discharge detector pens: They assume that every detected burst came from a bearing discharge in the equipment being tested. In 2014, a large motor manufacturer did a field study that, among other things, compared discharge detector readings with shaft voltage measurements, which are known to be accurate. They found that the detector agreed with shaft voltage 63% of the time: In 22% of the comparisons, the detector correctly predicted discharge, and in 41%, it agreed that no discharge occurred. But 30% of the time, it predicted discharge when the scope showed none. So these detectors evidently have a problem with false positive results – so much so that a positive reading is more likely to be wrong than right!
Common Mode Current Measurement
As we mentioned in our last post, it is impractical to directly measure bearing current in the field. So we recommend measuring shaft voltage, because it can unambiguously capture bearing discharge. Some consultants and manufacturers of VFDs and output filters recommend instead measuring common mode current (CMC) as an alternative. Like common mode voltage, CMC changes too quickly to be measured with a multimeter. It can only be measured with an oscilloscope and a current sensor called a Rogowski coil.
When you measure shaft voltage, it's easy to identify a discharge. But CMC includes all stray high frequency current through the motor. In small, properly grounded/bonded motors, only a small fraction of this current goes through the bearings – Most passes into the stator frame and then to ground or back to the drive. Measuring CMC may be useful in assessing the potential for bearing currents, but it cannot detect whether they are occurring.
This is shown the figure below, showing real data on CMC and shaft voltage levels. Notice the discharges shown in the shaft voltage – There is no hint in the CMC waveform that anything has happened. Simply put: Measuring common mode current cannot tell you whether a motor has bearing currents. Measuring CMC does have its uses, but detecting bearing current is not one of them, and as illustrated in the figure, low CMC does not mean low risk of shaft voltage discharge.
Conclusion
Shaft voltage testing is the gold standard of testing for bearing current. Discharge detection and common mode current measurements have their uses - both can be very helpful in measuring electrical noise (EMI/RFI). But neither of them can show what shaft voltage measurement can: the unambiguous presence of electrical discharge in bearings, and a measure of how much damage those discharges can do.