In 2009, the city of Hutchinson, Kansas opened its new Reverse Osmosis Water Treatment Center. The plant uses 17 pump motors, all controlled by variable frequency drives, to move water through the treatment process and to the city's supply towers.
Chronic Pump Motor Failure in a New Water Treatment Facility
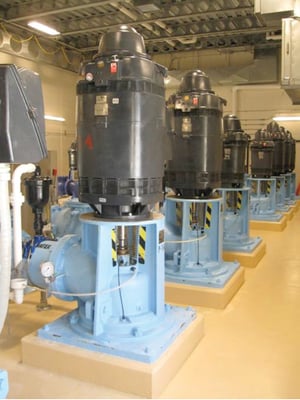
Two months after the plant came online, the pump motors' bearings began to fail. It started with a 250-hp vertical pump motor that began to squeal. The manufacturer replaced that motor's bearings, but soon other motors developed the same problem.
Something was clearly wrong.
What Was Wrong with the Motors?
The plant turned to a new motor repair contractor, Independent Electric Machinery Company. Independent Electric found the cause of the problem. The drives controlling the motors were creating voltage on the shaft. That voltage caused arcing through the bearings, producing pitting, roughening, and eventual failure. Luckily, Independent Electric had experience with electrical bearing damage.
What Was the Solution?
In fact, they had developed what they call the Vertical Motor Solution. This consists of isolating the thrust bearing and installing an AEGIS® Shaft Grounding Ring at the guide bearing. The AEGIS ring bleeds voltage safely off the shaft before it can arc, and the insulation prevents circulating currents.
In all, ten vertical pump motors had been damaged before they got the Vertical Motor Solution. After that, AEGIS rings and bearing insulation were installed on the other seven pump motors.
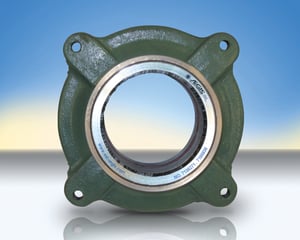
The bearings haven't failed since.
Why Choose AEGIS® Shaft Grounding Rings
This ordeal made an impression on Dan Biby, an engineer who helped design the plant and dealt with this problem.
He said, "We use the rings on all jobs to eliminate downtime, replacement, and installation costs. Installing rings can prevent these problems altogether. And the cost is insignificant when compared to the total project cost."
Over the years, motor manufacturers have become aware of this problem. Nowadays, both vertical and horizontal motors are available with AEGIS rings factory-installed. In fact, US Motors (Nidec) has made AEGIS rings standard in their Vertical HOLLOSHAFT® Inverter Duty motors (WPI and TEFC models).
AEGIS Shaft Grounding Rings have a 2-year extended warranty against bearing fluting damage. No other shaft grounding product offers a warranty like this.
To learn more about AEGIS shaft grounding and best practices for electrical bearing protection, sign up for a training. We offer monthly live training webinars, and we can also visit your facility to review your exact application.
This blog post is based on this case study.