The pulp and paper industry is a vital sector of the global economy and produces essential materials for everyday use. As in most other manufacturing sectors, rotating machinery – electric motors, pumps, conveyors, and more specialized equipment – plays an enormous role. This machinery’s rotation is made possible by bearings, which provide a low-friction interface between the rotating and stationary mechanical components. If a machine bearing fails, then so does the machine. A bearing failure in a critical machine can halt an entire production line. The costs of this unplanned downtime are enormous, often in hundreds of thousands of dollars per hour.
Bearings are prone to damage from various sources. In this blog post, we will look specifically at electrical bearing damage in pulp and paper mills and how it can be mitigated.
Causes of Electrical Bearing Damage in Paper Mills
Variable Frequency Drives
The most common cause of electrical bearing damage to rotating equipment is variable frequency drives (VFDs). While VFDs allow precise control of motors and the processing equipment they drive and allow large energy savings in variable speed/torque applications, the power they put out can damage motors. Particularly, because VFD output voltage is not balanced, it produces a voltage on the rotor (across the bearings). If this voltage gets large enough, it will discharge through the bearings of the motor or driven equipment. This discharge, which can occur thousands of times per second, roughens the smooth surfaces of the bearing and degrades the bearing grease. This damage accumulates over time and can shorten a bearing’s lifetime to just a few months.
VFDs control electric motors at every stage of pulp and paper processing, from hydrolysis, thickening, and pulping to pressing, drying, and calendering. The motors at every step of the process, as well as the pumps and gearboxes that they drive, are at risk.
One effective way to protect the motor and equipment bearings is to ground the motor shafts with AEGIS® Shaft Grounding Rings. Grounding rings dissipate the shaft voltage before it can build up enough to arc through the bearings. This protects the bearings from electrical damage, improves machine reliability, and helps ensure production uptime.
In larger motors, such as in this case study, a circulating type of bearing current also occurs, driven by an end-to-end shaft voltage. In these larger motors, one insulated bearing is necessary to interrupt circulating current, along with a shaft grounding ring for discharge current.
Static Electricity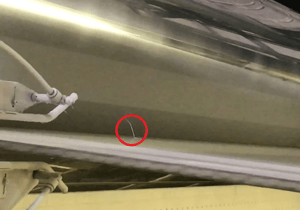
In the later, drier, stages of paper production, static electricity can build up on the rolls. In extreme cases, like in this case study, the static can build up high enough to arc through and damage calender or other bearings. Again, this weakness can be protected with AEGIS shaft grounding.
One advantage of AEGIS Shaft Grounding Rings is their 2-year extended warranty against bearing fluting damage. No other form of shaft grounding offers a warranty like this.
To learn more about AEGIS shaft grounding and best practices for electrical bearing protection, sign up for a training. We offer monthly live training webinars, and we can also visit your facility to review your exact application.