AEGIS Rings have worked for years to improve reliability and sustainable operatuion of HVAC and Pump motors. Case in point: Harvard University's Campus services Facility Maintenance Operations (FMO) "offers Motor Shaft Grounding, a maintenance program that prevents bearing failure and significantly extends motor life."
Variable frequency drives (VFDs) present a compelling option for energy savings in sustainable building projects. Power usage in continuously running centrifugal pumps and fans decreases notably with input modulation by a VFD. For example, a 20% reduction in fan speed can reduce energy consumption by nearly 50%. VFDs also introduce their own sustainability problems, however. VFD-induced shaft currents can damage bearings, leading to shorter motor life and costly repairs. Shaft grounding technology such as the AEGIS Shaft Grounding Ring offers a sustainable solution to this problem. Unfortunately, most new construction projects including VFD-driven motors do not utilize this effective option.
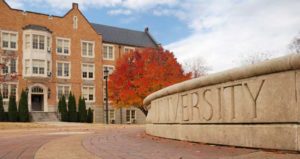
The university maintenance department has spearheaded a campus-wide sustainability drive starting with their own Platinum LEED certified headquarters. A major component of this has been a testing program for VFD-driven HVAC motors. Maintenance technicians employ oscilloscopes and voltage measuring probes to ascertain the presence of shaft voltage. When harmful voltage levels are detected, the maintenance department may recommend the installation of an AEGIS ring. Already successfully employed in multiple new buildings on campus, expanding the AEGIS ring to existing motor setups that require bearing protection continues to increase campus-wide sustainability.
The University Test Case
In December 2009, the ring's manufacturers installed their product on two VFD-controlled HVAC motors in the maintenance headquarters building as a demonstration of the new program. The identical three year old Baldor 7.5HP motors respectively powered a chilled water pump and an air supply fan. With the VFD set at 60HZ, the first motor was running at 1,776rpm. The oscilloscope measured peak-to-peak discharges of 61 volts. Results showed rapid voltage collapses at the trailing edge of the waveform, typical of the electrical discharges that damage bearings. After the reading, technicians cleaned the shaft and installed a split AEGIS ring. Follow-up test results displayed the discharge plot as a straight line, indicating that the AEGIS ring diverted shaft voltage discharges.
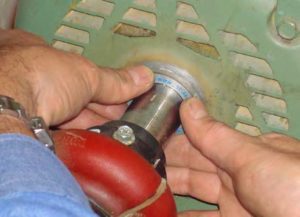
The second motor was tested under identical conditions and measured 50.8 volts peak-to-peak shaft discharge. Due to the limited accessibility of this motor, application of a hand-held heater sped epoxy curing in the AEGIS ring installation. After the complete installation, a new test read only 380 millivolts peak-to-peak, again indicating the AEGIS ring successfully diverted shaft voltage discharges to ground.
Conclusion
VFDs provide a compelling option for energy savings in sustainability-minded design. However, unless a product such as the AEGIS Shaft Grounding Ring mitigates the risk of bearing damage, repair costs could outweigh any savings. While this problem remains best addressed in the design stage of the system, the university case study effectively demonstrates the potential to retrofit previously installed motors with shaft grounding technology. Once installed, an AEGIS ring requires no maintenance and lasts for the life of the motor, providing effective protection against shaft voltage.
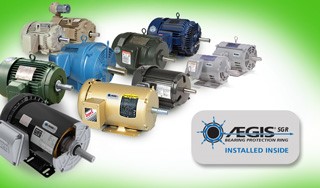
More information about the university case study can be found here.