Unlike asynchronous AC induction motors in which the speed of rotation is slower than the speed of the magnetic field, permanent magnet AC (PMAC) motors are synchronous machines that rotate at the same speed as the magnetic field produced by the stator windings. In doing so, they eliminate rotor conductor losses, offering significantly higher efficiencies and power factors, as well as improved performance and speed control. In fact, PMAC motor losses are typically 15-20% less than those of equivalent size NEMA premium induction motors. And they provide higher flux density than comparably-sized induction motors. Simply put, they deliver more power (torque) within a given physical envelope, or equal torque in a smaller package. They also have a wider speed range than AC induction motors.
PMAC motors are also known as Permanent Magnet Synchronous Motors (PMSMs) and Brushless AC Motors. These motors use rare earth permanent magnets, such as neodymium or samarium-cobalt, that have very strong magnetic properties and produce high flux levels in the motor. They are so strong, in fact, they can interfere with pacemakers, hearing aids, and other implanted medical devices, as well as electronic devices (cell phones, tablets, watches, etc.) and even credit cards. But once the rotor has been enclosed within the motor housing, radiated magnetic energy is no greater than that of an induction motor.
Virtually all true permanent magnet motors are operated by variable frequency drives (VFDs). Consequently, they are at risk of electrical bearing damage from VFD-induced shaft voltages, just like AC induction motors. And because they typically cost more than AC induction motors, they are more expensive to replace.
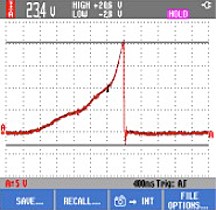
Lab testing of two PMAC motors (a 45 kW motor and a 300 kW motor) operated by pulse width modulated (PWM) VFDs illustrates that permanent magnet motors are not immune to electrical bearing damage caused by VFDs. Both motors were tested at 5000 RPM. The shaft voltage reading from the 45 kW motor with no bearing protection showed peak-to-peak voltage spikes of 21.8V. The waveform illustrates common mode voltage from the PWM drive capacitively coupled to motor shaft. The second reading was taken after installation of an AEGIS® Bearing Protection Ring on the motor. The smaller wave form demonstrates that the AEGIS® Ring dramatically reduced shaft voltages, channeling them away from bearings and safely to ground. In fact, the AEGIS® Ring reduced damaging shaft voltages by more than 70% (from 21.8V to 6.6V peak-to-peak) and eliminated EDM discharges through motor bearings.
When the same testing was repeated on a 300 kW motor, the results were even more impressive. The AEGIS® Ring reduced shaft voltage levels from 23.4V peak-to-peak to 4.8V peak-to-peak, a reduction of 80%. And the AEGIS® Ring also eliminated EDM discharges through motor bearings.
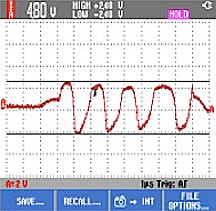
Field testing also demonstrated that shaft voltages and bearing currents were present on a new PMAC motor at levels sufficient to damage motor bearings. Readings taken from the shaft of an unprotected 5 HP PMAC motor operated by a PWM drive (designed for a
PM motor) showed common mode shaft voltage spikes (typical of bearing discharges) of 14.8V peak-to-peak as well as actual dv/dt bearing discharges of 12.1 volts. Once an AEGIS® Bearing Protection Ring was installed on the motor, voltage levels dropped to 3.28 volts peak-to-peak — a 78% reduction!
So, while PMAC motors offer many advantages over AC induction motors (higher flux density, more torque, greater energy efficiency, and wider speed range), they are every bit as prone to EDM bearing damage from VFD-induced shaft voltage discharges as AC induction motors. The good news, however, is that AEGIS® Shaft Grounding Rings are equally effective in preventing VFD-induced EDM bearing damage to these high-performance motors as they are in preventing such damage to AC induction motors.