Although we talk in this blog mainly about electrical bearing damage, there are plenty of other sources of damage and failure modes for motor bearings. Although there are several guides and schools of thought out there, we'll focus on one set of five sources of damage. The following is adapted from an article by SKF called 5 Most Common Causes of Bearing Failure in Electric Motors and What to Do About Them.
5 Sources of Bearing Damage in Electric Motors
In no particular order, they are:
Inadequate lubrication and contamination
Bearings spin at high speed, and without adequate lubrication, you will end up with metal-metal contact, causing wear, heating, and possible contamination of the lubricant. The first preventive measure is to check that the regreasing lubricant type, volume, and interval are appropriate. If there is contamination, check the seals. In some cases, a more-viscous lubricant may be needed. (It should be noted that over-greasing can also cause problems.)
Electrical erosion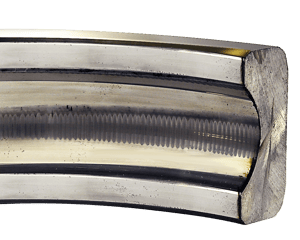
Regular readers of this blog won't be surprised to see this one on the list. Electric current, typically a side effect of variable frequency drive control, passes through the bearings. The end result is bearing fluting (image at right) and failure. This can be mitigated in several ways. Our preferred method - this being the AEGIS® blog - is to install an AEGIS Shaft Grounding Ring on motors under 100 hp/75 kW and an AEGIS ring and an insulated or hybrid bearing at the opposite end. Other approaches include two insulated bearings and an insulated coupling for the driven equipment or a sinewave filter capable of converting the drive's current and voltage waveforms to sinewaves. These solutions are effective but more expensive than shaft grounding.
Vibration
Motor bearings can be damaged by vibration, both during transportation and even while sitting in storage. The vibrations create marks in the bearing races called false brinelling (shown at right; which somewhat resembles fluting). This can be prevented during transport by locking the shaft axially with a flat piece of steel bent into a "U" shape while preloading the non-drive end and then radially locking the drive end with a strap. To prevent vibrational damage during storage, you can turn the shaft periodically so any vibrational contact is spread across the bearing surface (rather than building up into false brinelling).
Improper installation and setup
This can cause several types of damage. Common mistakes include using a hammer to couple the shaft to the load (which can cause true brinelling), misalignment, imbalance, applying excessive belt tension, and errors in mounting, causing overloading. To avoid these errors, always follow the recommended installation procedures and use quality instruments to determine alignment, tension, etc.
Insufficient load
Bearings need a minimum load to function properly. Inadequate load can be as damaging as excessive load. Damage from insufficient load appears as smearing on the rolling elements and races. This is especially important with cylindrical roller bearings since they are designed for larger loads. (This does not apply to preloaded bearings.)
It is worth pointing out that these damage modes are not mutually exclusive and may interact with each other. For instance, insufficient load may make electrical erosion happen faster (by allowing shaft voltage to build up higher before discharge occurs). Electrical erosion also contributes to lubricant contamination because the arcing chemically degrade the grease and releases microscopic metal particles into the lubricant.
Check With Your Bearing Manufacturers
If you'd like to learn more, most major bearing manufacturers - and several bearing distributors - have resources available on common causes, appearance, and prevention of bearing damage.
As for electrical bearing damage, AEGIS Shaft Grounding Rings have a 2-year extended warranty against bearing fluting damage. No other form of shaft grounding offers a warranty like this.
To learn more about AEGIS shaft grounding and best practices for electrical bearing protection, sign up for a training. We offer monthly live training webinars, and we can also visit your facility to review your exact application.