Commissioning agents ensure that the plans of the architects and engineers who designed buildings, systems, or processes are executed as intended and that their concerns are addressed before structures or systems are put into use. These professionals spend most of their time reviewing actual structures or systems to verify that they have been built or implemented as designed. But savvy commissioning agents also take the initiative to point out potential shortcomings in designs and explain the consequences of these shortcomings... before any oversights or omissions can result in expensive repairs or lost revenue for the building owner.
Many of the recommendations commissioning agents make are obvious — items shown in plans that were not installed or were installed incorrectly. Others are not so obvious... such as motors controlled by variable frequency drives (VFDs) that have destructive shaft voltages but are not protected against electrical bearing damage.
VFDs create harmful voltages on the shafts of the motors they control — voltages that can discharge through motor bearings, destroying them and costing owners huge sums in repairs and lost production or revenue.
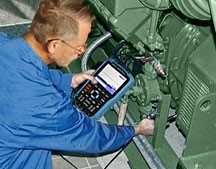
The best time to check motors to see if they are vulnerable to electric bearing damage is during the commissioning process. By taking shaft voltage readings from the spinning shafts of VFD-controlled motors, a commissioning agent would see immediately whether the motor is protected with shaft grounding or not.
Motors with effective shaft grounding — such as ones with AEGIS® Shaft Grounding Rings installed — exhibit a virtually flat waveform, indicating a continual discharge of shaft voltage at levels too low to cause bearing damage. Unprotected motors, on the other hand, exhibit a build up of voltage on the motor shaft to high levels, often 10-40 volts peak, followed by sudden violent discharges. These discharges blast fusion craters or pits into the metal bearing surfaces. Left unchecked, these discharges can lead to pitting, frosting (widespread pitting), fluting (washboard-like ridges on the bearing race), bearing grease degradation, and complete bearing failure — often in as few as 3 months!
The savings from preventing such damage can more than offset the cost of hiring a contractor to retrofit AEGIS Shaft Grounding Rings onto motors. Consider the following:
- Most motor bearings are designed to last for 100,000 hours, but motors controlled by VFDs can fail in as few as 720 hours of operation.
- When a large HVAC contractor ignored a specification that called for the installation of AEGIS Shaft Grounding Rings on all motors, the commissioning agent pointed out the omission to the building owner. The job involved 300 motors, and the contractor was forced to remedy the problem at a cost of $200,000!
- Motor failures caused by VFD-produced shaft voltage result in hundreds of thousands of hours of unplanned downtime each year in the US alone. In addition, these failures reduce the performance and mean time between failure of the OEM systems in which they are used.
- An HVAC contractor recently reported that, of the VFD-controlled 30-60 HP vane axial fan motors he installed in a large building project, all failed within a year (two within 6 months). Repair costs totaled more than $110,000.
- Several large pulp and paper companies surveyed noted that the VFD-controlled AC motors used in their plants typically fail within 6 months due to bearing damage.
- After testing AEGIS Rings on a VFD-controlled 50 HP "problem" fan motor — a motor that had suffered bearing failure 3 times — the engineering firm hired to test and tune the VFDs at the Time & Life Building in New York recommended installing AEGIS Rings on all 240 HVAC system motors in the building.
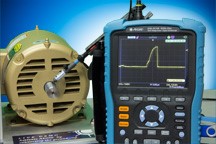
The best way to check for VFD-produced shaft voltages is to use an oscilloscope specifically designed to take such readings. The AEGIS Shaft Voltage Tester™ Digital Oscilloscope is specially designed and configured to take accurate voltage readings from the spinning shafts of motors. It comes complete with a special conductive microfiber-tipped probe, a probe holder with magnetic base, and a compact carrying case. The conductive microfiber probe tip provides exceptional electrical contact with the motor shaft. It is made from the same highly conductive microfibers as the brushes of AEGIS Shaft Grounding Rings.
If the motor specifications call for shaft grounding, a visual inspection of the motor may not be enough to verify that AEGIS Shaft Grounding Rings were installed. Since a large and growing number of motor manufacturers now offer motors with AEGIS Rings factory-installed inside the motor, shaft voltage testing is needed to verify that motors are protected - especially if the AEGIS Installed label is not visible. If readings indicate continuous low-level shaft voltage discharges, then the commissioning agent can feel confident that the AEGIS Rings were, in fact, installed.
If the motor specifications call for shaft grounding, a visual inspection of the motor may not be enough to verify that AEGIS Shaft Grounding Rings were installed. Since a large and growing number of motor manufacturers now offer motors with AEGIS Rings factory-installed inside the motor, shaft voltage testing is needed to verify that motors are protected - especially if the AEGIS Installed label is not visible. If readings indicate continuous low-level shaft voltage discharges, then the commissioning agent can feel confident that the AEGIS Rings were, in fact, installed.
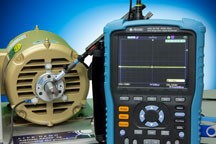
If design specifications do not call for shaft grounding on motors, the commissioning agent can prove his value by recommending that motors be retrofitted with uKITs — AEGIS Rings with universl mounting brackets. AEGIS uKITs were designed for fast, easy field installation around the shafts of coupled motors, and can accommodate shaft shoulders, slingers, and other end bell protrusions.
By making such a recommendation, the commissioning agent can help the building owner save the time, hassle, and expense of trying to fix a building or process problem... before it becomes a problem.
For more information on specifying bearing protection, click here.
For more information on the AEGIS Shaft Voltage Tester, click here.