As the problem of VFD-caused electrical bearing damage becomes better known, more electric motor users are looking for solutions. And more manufacturers are offering solutions. But most of these products can't solve the entire problem. For instance, AEGIS® Shaft Grounding rings are great at stopping damage due to shaft voltage discharge, but they cannot prevent circulating currents in larger motors. That's why for large motors, we recommend an AEGIS ring at one end (to take care of discharge currents) and an insulated bearing at the other (to block circulating currents). Together, they virtually eliminate the risk of electrical bearing damage.
There are many types of VFD output filters out there, but in this post, we are only speaking of purely inductive filters. Inductive filters are commonly called common mode chokes or common mode cores, and occasionally inductive absorbers, and some brands claim to completely solve the problem of electrical bearing damage from VFDs. But do they?
The short answer is: No. These products can reduce damage due to high frequency circulating currents and rotor ground currents, but they cannot eliminate bearing damage due to shaft voltage discharge. To understand why, we'll have to look at the VFD output power, and three kinds of electrical bearing damage.
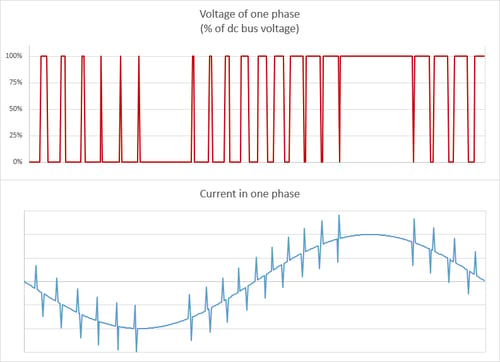
VFDs convert line power into a series of pulses of voltage in each phase (Figure 1, top). By controlling the timing of each pulse, the drive can run the motor at speeds much slower than the line frequency. But unlike line voltage, drive output voltage is not balanced. The pulses in each phase do not cancel each other, the way that line voltage does. The three phases' average value is called the common mode voltage.
The common mode voltage is a measure of the total (net) voltage that the motor "feels". This net voltage induces the shaft voltage that causes rotor discharge bearing currents. Rotor discharge currents are a problem in all motors on drives, regardless of size.
The current from a drive looks less like a pulse and more like a sine wave (Figure 1, bottom). But every time the drive switches on or off, there is a spike of high frequency current, as the rapidly changing voltage charges capacitances in the motor and cabling. Between the three phases of drive power, the current mostly cancels out. Except for those spikes. The sum of the current spikes in each phase is called the common mode current.
When common mode current gets to the motor, it doesn't go through the stator windings because they have high impedance (resistance) to high frequency current. Instead it leaks by capacitance from the windings to the motor frame, and then runs to ground (and back to the drive). This can cause bearing damage in two ways.
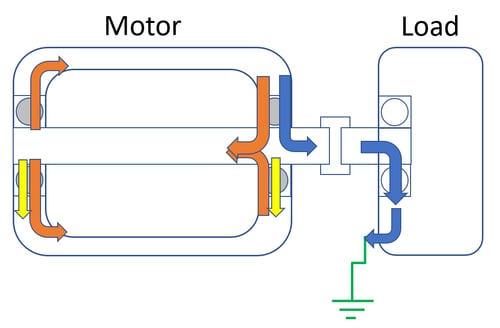
In motors over 100 hp (75 kW), common mode current produces high frequency circulating currents. These are larger than rotor discharge current, and they damage the bearings faster. They are not a problem in smaller motors.
In poorly grounded motors, there is no low-impedance path back to the drive. So much of the common mode current will arc through the motor bearings, run down the shaft to the driven equipment, arc through the equipment's bearings, and then run to ground and back to the drive. This is called rotor ground current, and it damages motor and other equipment's bearings. Rotor ground current is even larger than circulating currents. It can be a problem in all motors on drives, but only if they're poorly grounded.
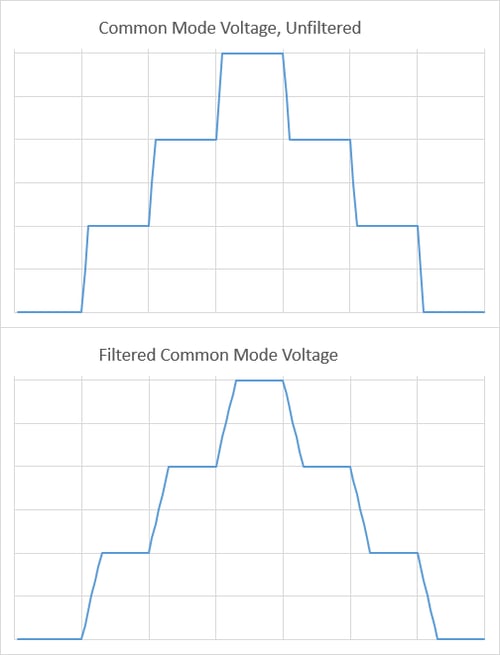
Inductive filters can reduce the common mode current by 10 to 65%. So they can absolutely reduce the damage due to high frequency circulating and rotor ground currents. We recommend one insulated bearing to block circulating current, and a high frequency grounding strap to avoid rotor ground current. But these filters are definitely better than no protection against circulating and rotor ground currents.
These filters reduce common mode current. But they barely affect the common mode voltage, the cause of rotor discharge currents. They may reduce the voltage by up to 15%, but they mainly only decrease how quickly it changes. What matters for rotor discharge currents is the SIZE of the common mode voltage, not how quickly it rises. See Figure 3.
Because the common mode voltage is not reduced, the shaft voltage is not reduced. Some distributors and marketers of these filters specifically say that the shaft voltage should not be measured. "Pay no attention to the man behind the curtain!"
So with or without inductive filters, you will still get shaft voltage discharge through the bearings... Unless they're protected with effective shaft grounding. Like an AEGIS ring.
AEGIS Rings also come with a 2-year extended warranty against bearing fluting damage. No other form of protection against VFD-caused bearing damage offers a warranty like this.
To learn more about AEGIS shaft grounding and best practices for electrical bearing protection, sign up for a training. We offer monthly live training webinars, and we can also visit your facility to review your exact application.
Note: In addition to the purely inductive filters described here, there are also inductive + capacitive (LC or LRC) filters like dV/dt filters and sine filters. These can also reduce high-frequency circulating and rotor ground currents. There is a third type called a four-pole or all-pole filter, which is an LC filter with additional circuit elements linking each phase to ground or back to the drive's dc bus. This third type can accurately be called a common mode voltage filter, and it can minimize all VFD-sourced bearing currents. These filters, however, have their own drawbacks, including large size, high cost, and significant voltage drop (sometimes over 10%).