It was a packed house as the editors of Design News presented the 2017 Golden Mousetrap Awards, held in conjunction with Pacific Design & Manufacturing in Anaheim, Calif.
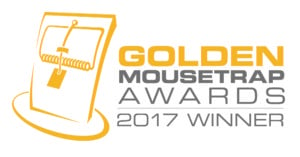
The Golden Mousetrap Awards were created to acknowledge and recognize American people, companies, and technologies driving innovation in the industry. Last night’s festivities, which also recognized Design News’ Lifetime Achievement Award winner, were a celebration of manufacturing and innovation in North America by honoring the companies and individuals who impact the industry through their hard work and groundbreaking ideas.
“We [at Design News] are honored to recognize those companies and individuals who have demonstrated a drive for excellence in their respective fields,” said Suzanne Deffree, content director and editor-in-chief of Design News . “The future of engineering and manufacturing is truly innovative, as the companies and individuals celebrated at the 2017 Golden Mousetrap Awards have shown the leadership and direction needed to push the industry to new heights.”
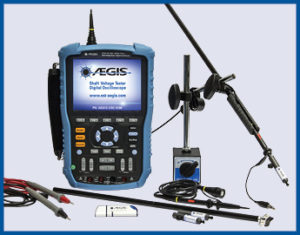
In the Electronics & Test: Test & Measurement Category, the AEGIS Shaft Voltage Tester Digital Oscilloscope from Electro Static Technology was chosen as the winner!
The AEGIS® Shaft Voltage Tester™ Digital Oscilloscope is an innovative system used to measure whether destructive shaft voltages exist on the shafts of motors controlled by Variable Frequency Drives. It is a Digital Oscilloscope with Conductive Microfiber Probe Tips that can measure the voltage on the spinning shaft of a motor.
It answers the question: Is your motor safe from destructive shaft voltages and electrical bearing damage?
Electrical Bearing Damage: Capacitive coupling between windings and rotor can create voltage on a motor's shaft — voltage that can discharge through bearings, damaging them and shortening motor life. For motors controlled by variable frequency drives, however, these voltages can be as high as 10-40 volt peak. At these higher levels, voltages can easily cause electric electrical discharge in the motor bearings, causing pitting, fusion craters, and fluting, which eventually lead to premature bearing and motor failure.
Until now, the only way to tell whether a motor was at risk for such bearing damage was to buy, rent, or borrow an oscilloscope and then buy some type of shaft voltage probe. Now, for the first time, there is a total shaft voltage detection system available in one package.
Used by Plant Maintenance, Facility Managers and Commissioning Agents:
With the AEGIS® Shaft Voltage Tester™ Digital Oscilloscope, plant maintenance personnel, facility managers and also new equipment commissioning agents can take shaft voltage readings from motor shafts quickly and easily – readings that confirm or deny the presence of shaft voltage discharges that can damage motor bearings. Users who already have a 10X oscilloscope with bandwidth at least 100 MHz may be able to measure shaft voltage with it and an appropriate set of our Shaft Voltage Probe™ Tips.
High amplitude EDM discharge pattern – Evidence of a Bearing Discharge
Typically EDM discharges can occur from 6 volts peak to 80 volts peak depending on the motor, the type of bearing, the age of the bearing, and other factors. The waveform image shows an increase in voltage on the shaft and then a sharp vertical line indicating a voltage discharge. This can occur thousands of times in a second, based on the carrier frequency of the drive. The sharp vertical discharge at the trailing edge of the voltage is an ultra-high frequency dv/dt with a typical "discharge frequency" of 1 to 125 MHz (based on testing results in many applications).
Damage caused by Bearing Discharges - Lead to Critical Motor Failure
Because of the high-speed switching frequencies in PWM inverters, variable frequency drives induce shaft currents in AC motors. The switching frequencies of insulated-gate bipolar transistors (IGBT) used in these drives produce voltages on the motor shaft during normal operation through parasitic capacitance between the stator and rotor. These voltages, which can register 10-40 volts peak, are easily measured by touching an oscilloscope probe to the shaft while the motor is running.
Reference: NEMA MG1 Section 31.4.4.3
Once these voltages reach a level sufficient to overcome the dielectric properties of the bearing grease, they discharge along the path of least resistance — typically the motor bearings — to the motor housing. During virtually every VFD switching cycle, induced shaft voltage discharges from the motor shaft to the frame via the bearings, leaving a small fusion crater (fret) in the bearing race. When this event happens, temperatures are hot enough to melt bearing steel and severely damage the bearing lubrication.
These discharges are so frequent (millions per hour) that before long the entire bearing race becomes marked with countless pits known as frosting. A phenomenon known as fluting may occur as well, producing washboard-like ridges across the frosted bearing race. Fluting causes excessive noise and vibration, and in heating, ventilation, and air-conditioning systems, it is magnified and transmitted by the ducting. Regardless of the type of bearing or race damage that occurs, the resulting motor failure often costs many thousands or even tens of thousands of dollars in downtime and lost production.
Failure rates vary widely depending on many factors, but evidence suggests that a significant portion of failures occur only 3 to 12 months after system startup. Because many of today’s AC motors have sealed bearings to keep out dirt and other contaminants, electrical damage has become the most common cause of bearing failure in AC motors with VFDs.