Along with solar power, wind power is the fastest-growing renewable energy source. Wind turbine generators work by capturing energy from the wind and using it to spin the generator shaft, producing electric power. These generators use a gearbox and an inverter drive (a.k.a. VFD) to match the power output's frequency to grid power's 50 or 60 Hz. Most also use inverters to excite the generator, while others use permanent magnets.
VFDs, Stray Voltage, and the Generator Shaft
But VFDs also create voltage on the generator shaft. This voltage will discharge to ground by any available low-resistance path. Unfortunately, these paths usually lead through the generator or gearbox bearings. Discharge through these moving parts causes cumulative electrical discharge machining damage. In bearings, the damage is called fluting; in gearboxes, it's called tiger-striping. Whatever you call it, electrical damage causes generator failure. And failure means expensive repairs and downtime.
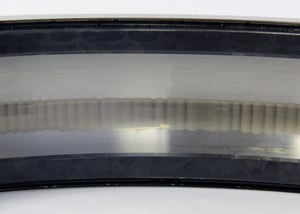
Wind Generator Electrical Bearing Damage
Most generators have hybrid or insulated bearings that resist electrical damage from discharge and circulating currents. But coupled equipment, like gearboxes and tachometers, is left vulnerable. So wind generators also include rotor grounding to reduce the risk to this equipment. Inverter-excited generators use a carbon shaft grounding brush, and permanent magnet designs use rollers on the brake disk. Both methods provide a low-resistance path to low-frequency and DC current. So this otherwise destructive current goes harmlessly through the brush or roller.
But shaft voltage contains high and low frequencies, and brushes and rollers have high impedance (resistance) to high-frequency electricity. So even with a brush or roller, the system is still at risk of electrical damage. Wind turbine generators also need a form of shaft grounding with low impedance at high frequencies.
Does a Wind Turbine Need Shaft Grounding?
The short answer is yes, and AEGIS® Shaft Grounding Rings are part of the solution. AEGIS PRO Series Rings surround the shaft with hundreds of thousands of conductive microfibers. These fibers have a high surface area, which gives them low impedance to high-frequency current.
With hybrid bearings to block circulating currents, a roller or carbon brush to carry dc and low-frequency current, and an AEGIS Ring for high frequencies, the system is fully protected against electrical bearing damage.
In the Field: Testing for a Wind Generator Manufacturer
Jens Leipner, the AEGIS Sales Manager for Northern Europe, recently went up-tower to do testing for a wind generator manufacturer. The test site was a 455-foot tall turbine (140m) turbine with 440-foot blades. The generator itself was a permanent magnet/VFD model. It had rollers on the brake disk for low-frequency grounding and a "violin string" shaft grounding device for high frequencies.
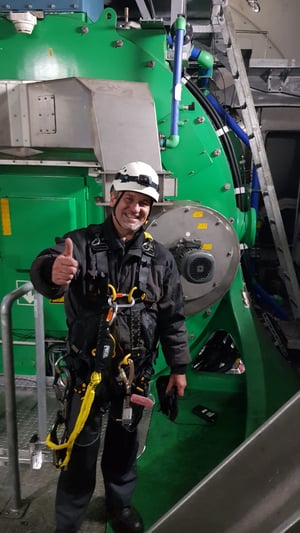
With no shaft grounding, the shaft voltage was 20 volts peak to peak. With the shaft grounding string, the voltage was brought down to a little over four volts. This is a safe level, but the grounding string showed severe wear. Because these devices are pressed, under tension, against a spinning shaft, they can quickly wear through.
When AEGIS PRO Ring segments were installed, the shaft voltage was decreased to safe levels of less than a volt. Further, the AEGIS Ring's fibers are not under tension; they only press lightly against the shaft. This makes them much longer-lived than grounding strings.
With long lifetimes and low impedance at high frequencies, AEGIS grounding rings are wind turbine generators' most effective grounding systems for high-frequency shaft voltage.
AEGIS Rings also come with a 2-year extended warranty against bearing fluting damage. No other form of protection against VFD-caused bearing damage offers a warranty like this.
To learn more about AEGIS shaft grounding and best practices for electrical bearing protection, sign up for a training. We can visit your site and give an in-person training with an emphasis on your specific focus. We also offer monthly live training webinars.