A new preventive maintenance program at a leading New England Ivy League university demonstrates how the push for more sustainable “green” building management has led to a growing awareness of a chronic, widespread problem with HVAC motors — electrical bearing damage and failure.
University Improves Sustainability of HVAC Motors in Platinum LEED® Building
Read and download the case study
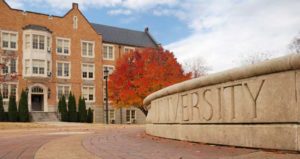
Shaft currents induced by VFDs can wreak havoc with bearings, dramatically shortening motor life and causing costly repairs. To mitigate these currents and realize the full potential of VFDs, a reliable method of shaft grounding is essential.
The university maintenance department has already used the AEGIS® ring successfully for fan and pump motors in several new buildings on campus. The AEGIS ring is available in two versions — a continuous ring or a split, and both versions can be installed with either brackets or conductive epoxy. The split ring (used in the university’s retrofit program) simplifies and speeds field installations because it can be installed without uncoupling attached equipment.
Local Motor Shop Helps Kansas Water Authority Solve Bearing-Damage Problem
Read and download the case study
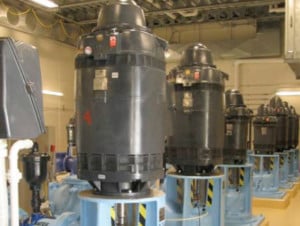
Electrical engineer Dan Biby of Professional Engineering Consultants (PEC), Wichita, KS, helped design the new Reverse Osmosis Water Treatment Center for the city of Hutchinson, Kansas. With the capacity to pump 10 million gallons of drinking water daily, the plant is the solution to a groundwater contamination problem.
“We use the [AEGIS] rings on all of our jobs to eliminate downtime, replacement, and installation costs. Installing rings can prevent these problems altogether. And the cost is insignificant when compared to total project cost.”
Pumps lift contaminated water from beneath an industrial area and remove most of its volatile organic compounds (VOCs) through reverse osmosis and aeration. The water is then diluted with uncontaminated water from wells across town before being pumped to the city’s supply towers. All of the pump motors are controlled by VFDs that provide adjustability in flow rate and pressure.
Making Motors Sustainable at Time & Life Building
Read and download the case study
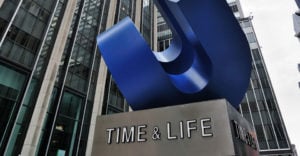
New York City
A preventive maintenance plan that reduces the total life-cycle cost of operations in a prominent building at the heart of New York City serves as a good example of how the push for more sustainable, green, building management has led to a growing awareness of a chronic, widespread problem with HVAC motors – electrical bearing damage.
Once installed, the AEGIS SGR requires no maintenance. Unlike conventional shaft grounding brushes, its conductive microfibers work with virtually no friction or wear; are unaffected by dirt, grease, or other contaminants; and last for the life of the motor regardless of rpm. Test results show surface wear of less than 0.001" per 10,000 hours of continuous operation and no fiber breakage after 2.5 million direction reversals.
AEGIS Rings also come with a 2-year extended warranty against bearing fluting damage. No other form of protection against VFD-caused bearing damage offers a warranty like this.
To learn more about AEGIS shaft grounding and best practices for electrical bearing protection, sign up for a training. We offer monthly live training webinars, and - pandemic restrictions permitting - we can also visit your facility to review your exact application.